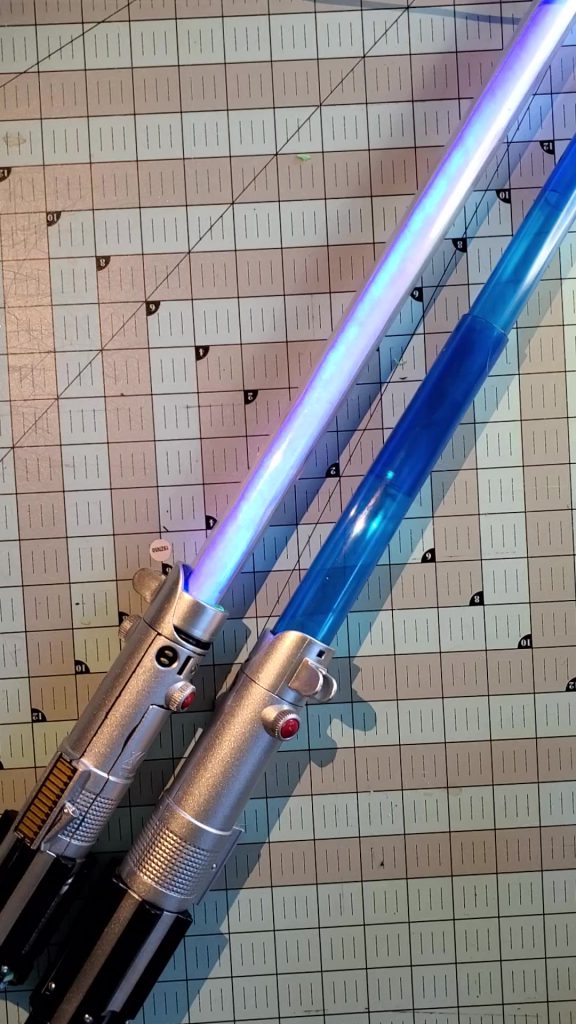
The pandemic showed us the large gaps of technology and internet access across social-economic groups, from people working out of a car due to unreliable home internet, to students managing limited use of the only computer in the household, sharing with parents, siblings, etc.
With the pandemic-related closures, makerspaces, and relevant tools such as 3D printers, laser cutters and power tools, all were inaccessible.
The result is an award-winning prop and guide for anyone to make a lightsaber with low-cost use.
How can one design & build a lightsaber with sustainable, low-cost methods?
Role: Sole designer, builder, researcher
Methods
Goal
- To inspire those with limited access to expensive tools, to craft and build
- To champion and support sustainability methods in making
Problem
- To make a lightsaber using upcycling/reuse methods, and low-cost accessible, inexpensive tools
- To document the design process to increase accessibility to make/craft a lightsaber
Participants
The immediate audiences include the Make: Media and Nvidia judges evaluating all submissions to the May the 4th Maker challenge. More broadly, my audience are novice crafters, makers, and electronics-interested Star Wars fans who want to make their own lightsaber while in the pandemic.
Design
This project is a series of trial and error, with the challenge of using inexpensive and accessible tools and methods. I also saved a lightsaber toy from the trash, and decided to carve out space for enhancing the lightsaber with improved sounds, lights and interaction. To be as sustainable as possible, I reused as much of the original toy as possible.
Role
Sole Researcher, Designer, Builder and Writer
Duration
1 month
Tools
- Dremel/rotary tool
- Microcontroller
- Speaker
- Soldering iron
- Vices, grips
- Wire stripper
Skills
- Design processs (research, prototyping, iteration)
- Electronics (soldering/wiring/etc)
- Arduino programming
- Power tools (rotary tool)
Insights
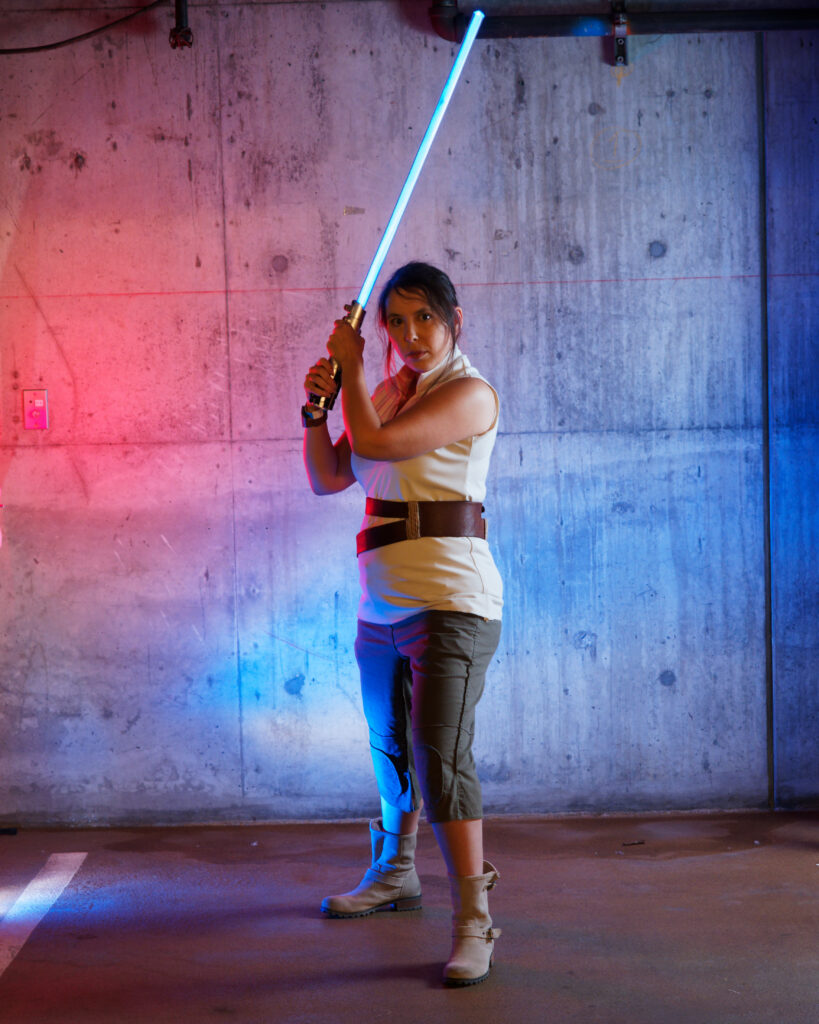
This build and resulting tutorial won Make Media & Nvidia’s May the 4th Maker Challenge, Best Cosplay/Prop. Here’s the award-winning submission and tutorial.
Carving as a low-cost method compared to 3D printing
While many lightsaber builds rely on a 3D printer, doing subtractive work and infinitely carving and sanding out a toy, was repetitive and calming. I had a tangible, good idea of what to carve, and went through countless iterations of carving, fitting, marking and carving again.
Both supporting fan communities and subverting companies
Multiple lightsaber community members consistently suggested I just buy a kit from known fan-based companies, for 10x my original cost, and no quantitative evidence that it was better in any metric. It reveals how pervasive these companies are to the community, and how my build both supports more low-cost, DIY builds, and inadvertently challenge those companies.
Reflections
When I debuted this lightsaber at SiliCon 2020, it was compelling that my lightsaber was similar in presence to more expensive, high-quality, metal lightsabers. To my surprise, I had multiple people guess at what kit/brand my lightsaber was made from!
This process continues to advocate for a do-it-yourself approach to prop-making; while chips, electronics, and parts were both cost-prohibited and in low supply during pandemic, I was able to make a high-quality lightsaber for less than $50, all with accessible tools and materials.
I actually improved the design further by making the lightsaber so bright, any photographer can capture it and no require additional touch-ups, giving a novice photographer a great photo with little effort.